
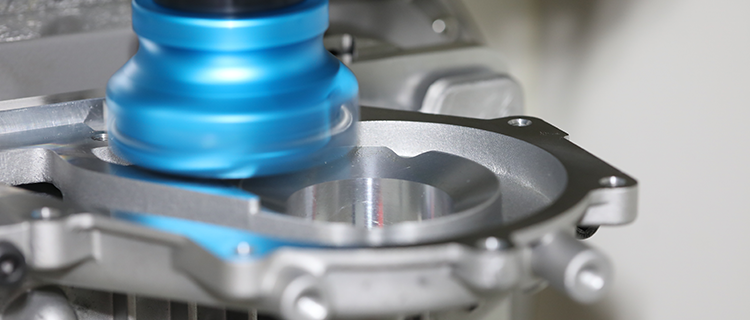
Die casting products play a very important role in automotive components. However, due to the characteristics of die casting process, die castings have poor dimensional consistency. Moreover, with the trend of lightweight and integrated requirement in recent years, it’s even more difficult to realize batch processing of features on die castings. As the common mode to process die castings is either adjust each piece manually or need specialized personnel to write code for alignment in control system. However, Jingdiao’s solution is convenient and effective. All you need to do is programming a measuring path in Jingdiao software with a few steps, and alignment will be automatically done in machine tools so that continuous batch production can be carried out. Considering the time you spend but still hard to have good accuracy, Jingdiao’s solution is your best choice.
Example Workpiece
Machining Center
Specialized in multi-axis positioning machining and 5-axis simultaneous machining of precision parts and complex hardware with high-efficient and high-quality machining performance.
Brake mechanism equipped on both axes ensures high rigidity when positioning;
Standard capacity of tool magazine is 36 sets, tool changing time is shorter than 1.2 sec;
Intelligent 5-axis workpiece alignment is achievable due to the application of OMIM technology;
Composite processing capability includes milling, grinding, drilling, tapping and other processes;
Large window is installed on front door to observe processing.
Technology
The way we realize automatic alignment for die casting is aligning program coordinate with workpiece coordinate through measuring the real position of workpiece and comparing it with theoretical one. This can be done due to OMIM technology, because it integrates software, control system and machine tools. After designing measurement strategy in software and output it into machine tool. The real position of workpiece will be measured, and the offset between real and theoretical position is calculated automatically. Position compensation function is enabled in control system, so that the error between two coordinates can be corrected. Besides this, position errors between features can also be eliminated through processing one feature based on the relative position to another feature after measuring and building a local coordinate.
+ READ MORE
LEARN MORE
Software
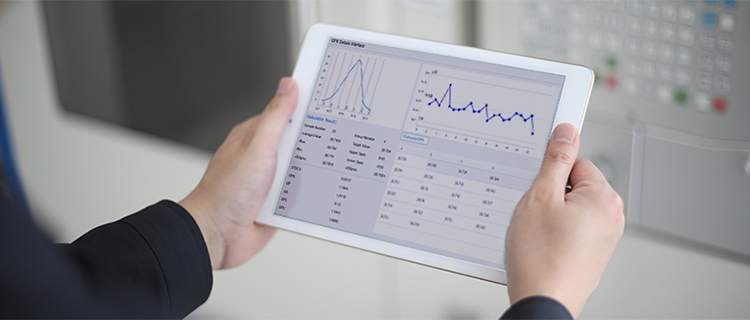
Functions include build measurement coordinate and feature measurement are provided in Jingdiao CAD/CAM software to replace the complex coding writing work and design measurement strategy to align workpiece. You only need to take four steps, which are select the features to be inspected, generate measurement path for each feature, select measurement path for each feature, generate the measurement path for alignment. Your operation will be guided by hints in software which also makes the output measurement program more secure, efficient and error-prone.
+ READ MORE
LEARN MORE
Service
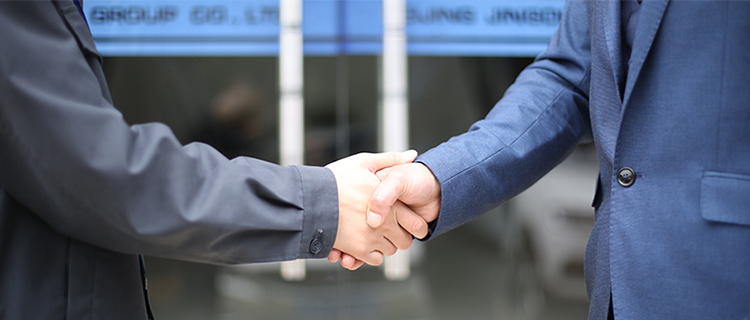
Machine selection service, customization and upgrade, engineering service and technical training are available for you. Do not hesitate to contact us.
Know more, rest assured more.
LEARN MORE